

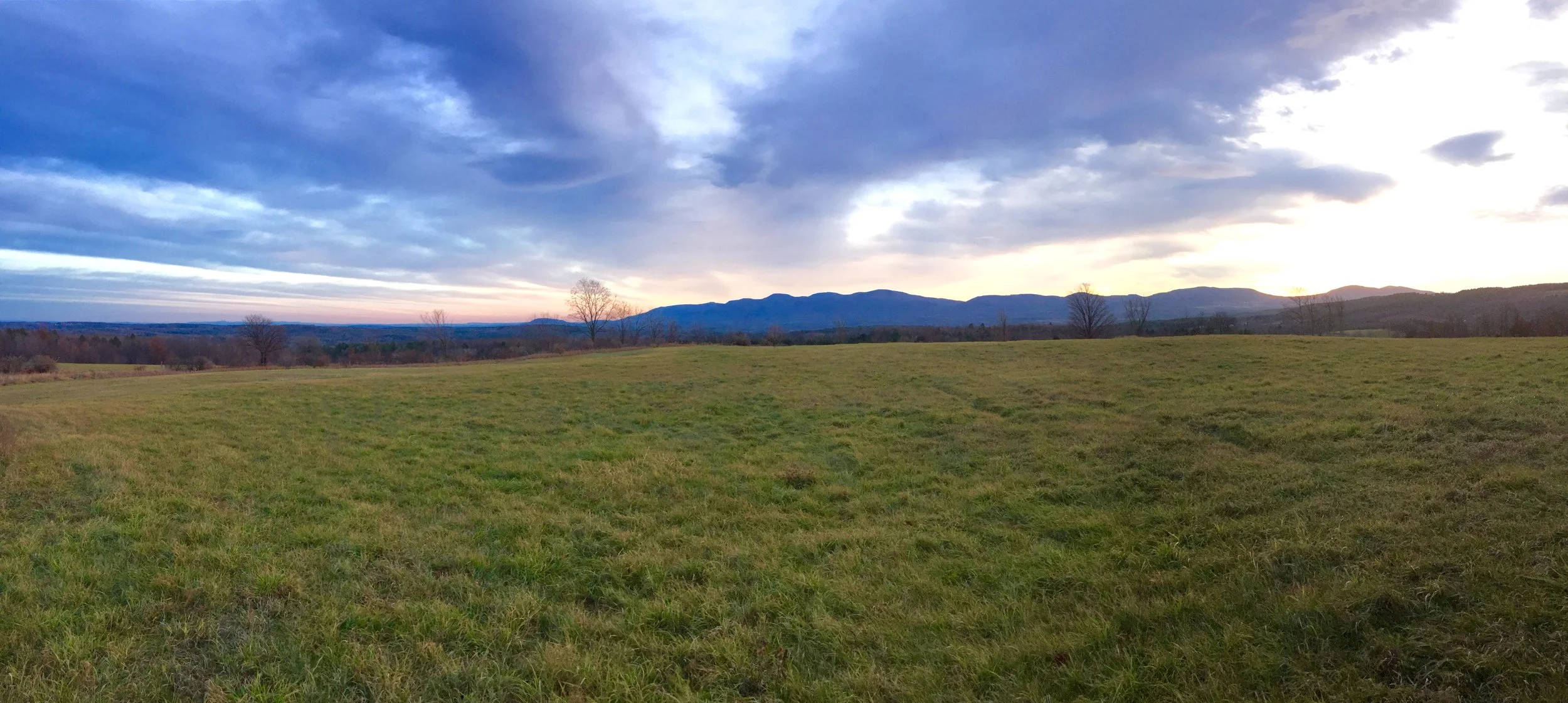
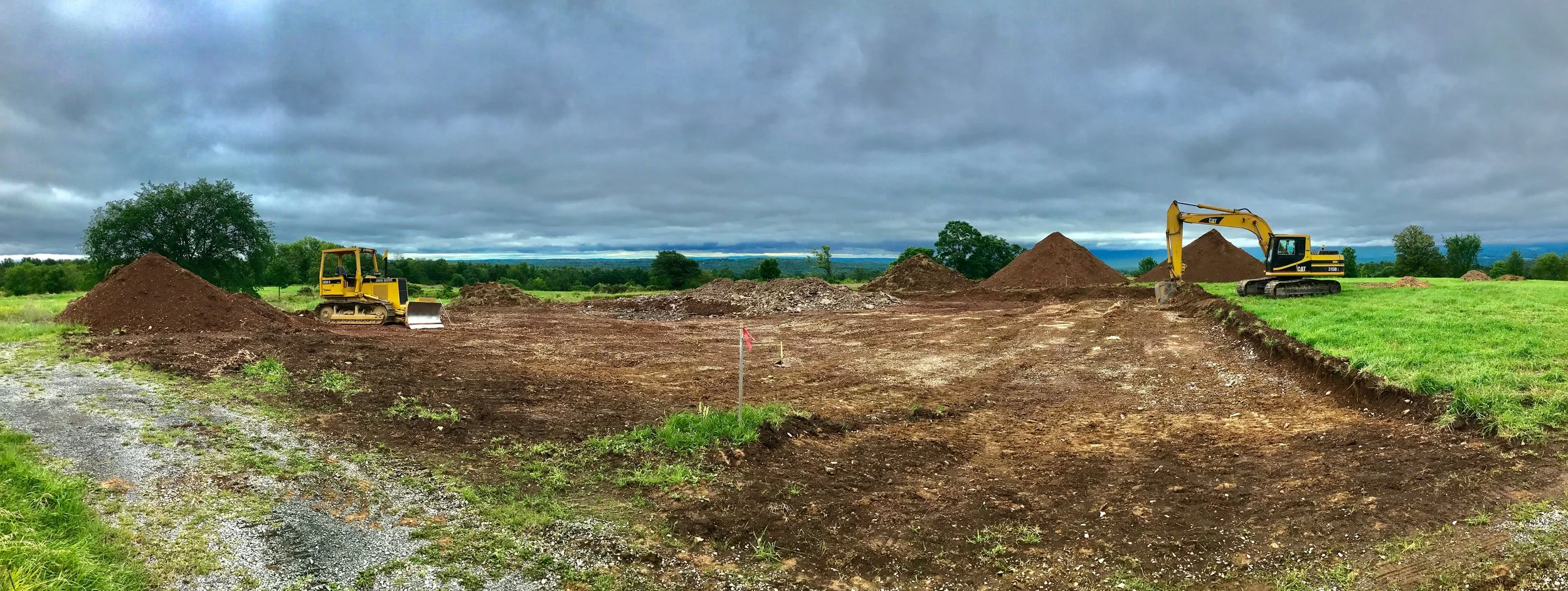








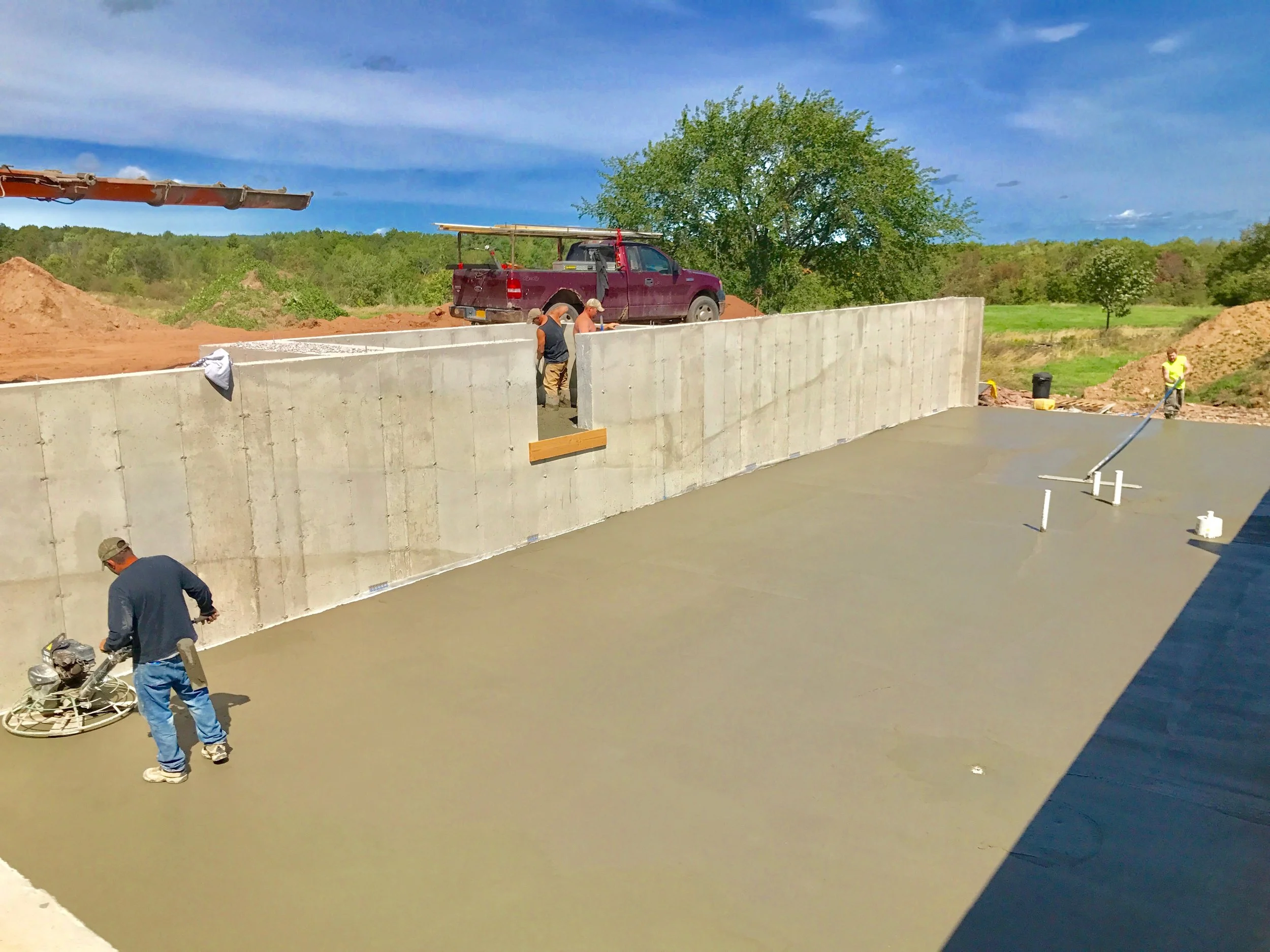




























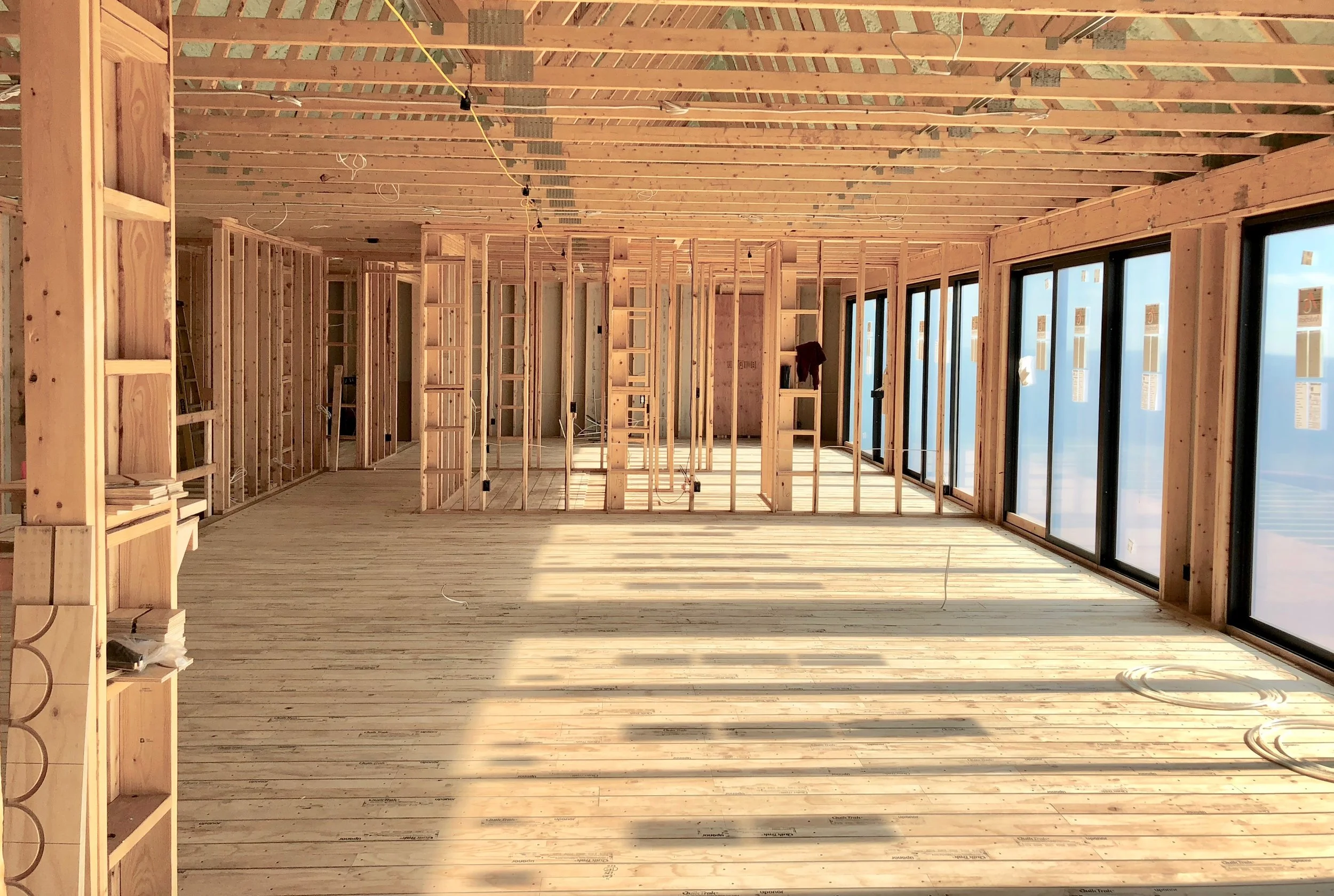




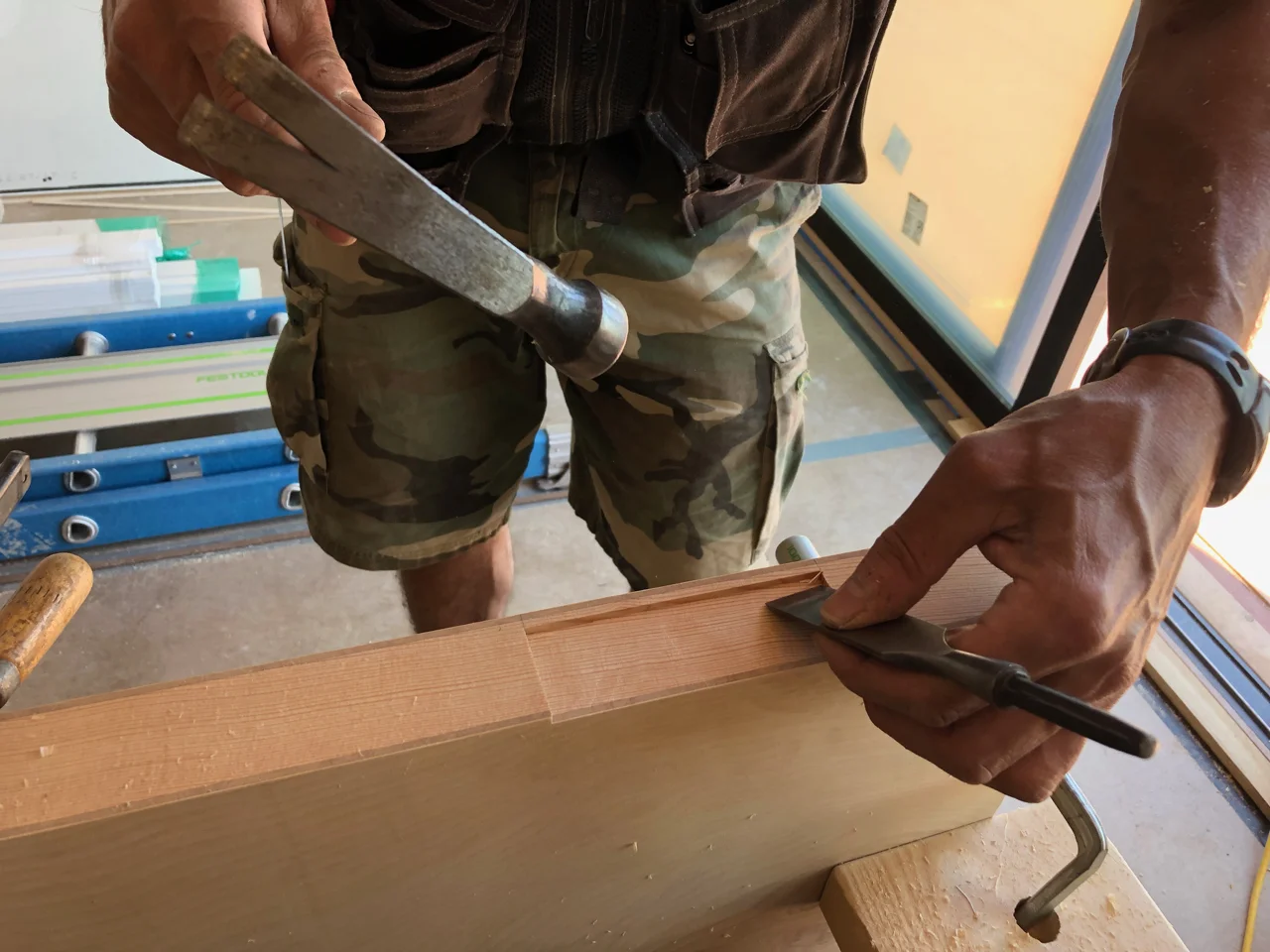







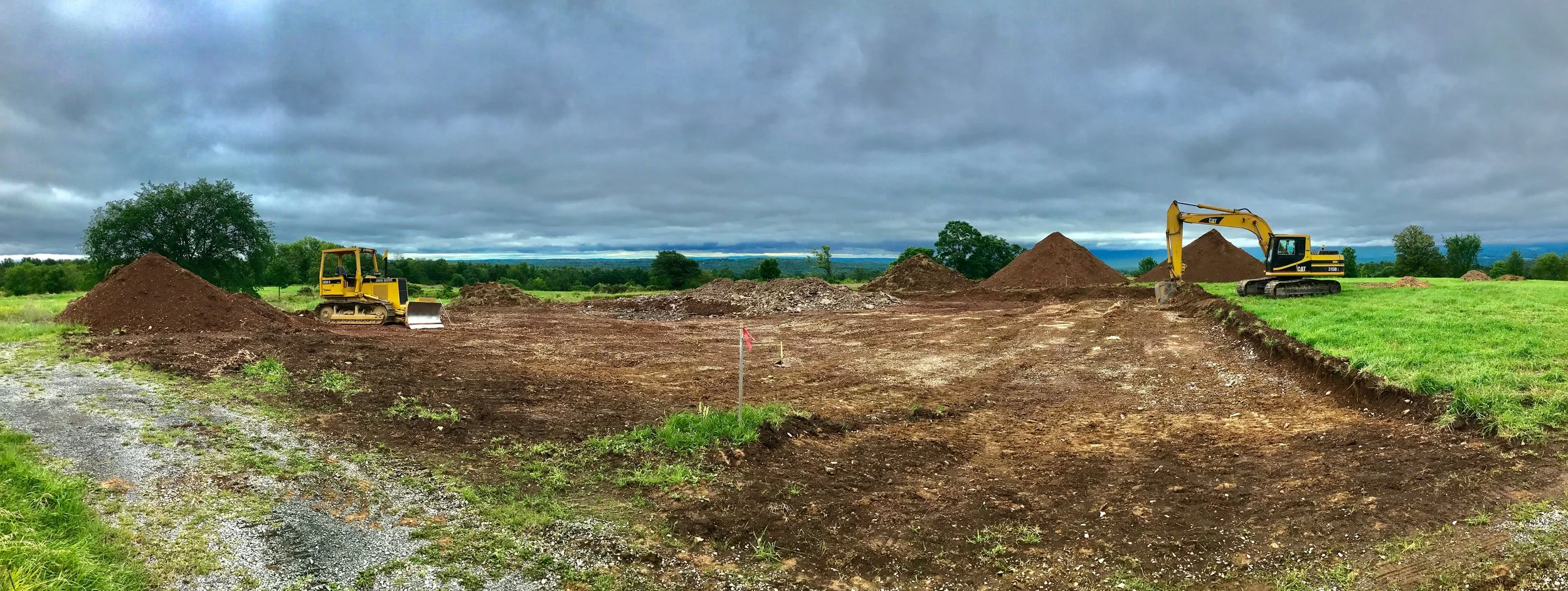
Careful planning and staging of excavated materials precludes the need to buy fill later.
First we scraped-off the turf--which will compost on site. Then we removed the rich topsoil--which we will preserve for the the final grading. Under the top soil, but above the rock layer, was a layer of dirt and clay that was saved to underlay our final grading prior to topsoil.

Placing concrete is daunting work done quickly and efficiently with a reputable masonry firm. The goal is plumb, level, and square. The devil, however, is in the subsequent, hidden details. A high-performance foundation has redundant waterproofing details inside and outside the walls and floor. A completely insulated and moisture-proofed envelope is what you're looking for--all to be hidden away for the life of the structure.

A matrix of materials and details set the stage for radiant heating tubes and the concrete slab.
Radiant heating tubes carefully installed and ready for concrete placement.

Wall panels were fabricated in a factory for precision. And because the wood structure is made indoors, the vulnerable materials are not subjected to the whims of nature on the job site. The precision-made components yield far less waste than site-built structures as well. However, the biggest selling point of a panelized home comes from a quick “dry-in” time.. The less time fragile materials are subjected to the elements, the better the final product. Incredibly, the floor system and walls were installed in one day. It was four more days until the home was completely dried-in.

Metal roofs have numerous advantages over other roofing products. But one of the main advantages is life-cycle. It is possible to have a trouble-free metal roof for 50 to 100 years. We are using Galvalume not only for it's beauty, but it's Energy Star reflectivity qualities.
Galvalume steel sheet is carbon steel sheet coated with aluminum-zinc alloy by a continuous hot-dip process. The nominal coating composition is 55% aluminum and 45% zinc.

Our siding is locally harvested Eastern Hemlock. We are using re-sawn, kiln-dried ship lap straight from the sawmill. No finish will ever be applied to this material. No finish means no maintenance. We maximize the life of the siding by using a rain screen detail that allows constant air circulation on the backside of the wood. This allows for the material to air-dry from both sides.

Having a clean, level area outdoors and off the ground is always a good idea. Build the deck right away and you have a loading dock, staging area, and easy access to install doors, siding, and roofing.

Careful planning maximizes material yield thus reducing waste. This saves the planet’s and the customer’s resources.

Cor-ten steel was selected for the deck railing. Like the siding, the material was selected to age naturally—never needing to be maintained. The “finish” in cor-ten is a natural patina of rust that actually strengthens the steel. The custom stainless steel cable rail system was used to maximize the view from inside the house.

Using local materials like this quarried limestone can give a unique appearance for less cost.

We used wide-plank flooring from Admonter coupled with the Sika AcouBond®-System. This system works extremely well with wood flooring over radiant heating tubes to provide a stable, permanent bond—coupled with an unrivaled sound transmission coefficient (STC). STC is a measure of sound transmission between floors. We love using engineered flooring primarily because it preserves our precious hardwood forests as well as guarantees that the flooring will always remain flat.

As of October 3, 2016, all new Residential Construction must comply with ACH 50 or the so called “Blower Door Test.“ This test requirement assures that the code required maximum allowable air leakage is not exceeded. The maximum allowable rate of air leakage as verified by the ACH 50 test is 3.0 Air Changes per Hour (ACH).
Although 3.0 ACH is considered a “tight” house, we always tighten up a house to exceed the highest standard in modern construction: the German Passivhaus standard of 0.6 ACH 50. This guarantees the greatest efficiencies in heating and air-conditioning—again saving the planet and the homeowner over the long run.
Our final number? An astonishingly tight 0.26 ACH at 50 Pascals.